UF Engineers Purposely Rammed a Bridge to Better Understand How to Design Safer, Less Expensive Bridges
By Aaron Hoover
downloadable pdf
For a guy who has spent years researching the development of safer, less-expensive ways of building bridges, a barge ramming a bridge in the Florida Panhandle might seem like a disaster.
But for Gary Consolazio, it was all part of the plan.
Actually, the barge rammed the decommissioned, 1960s-era St. George's Island Bridge spanning Apalachicola Bay 15 times in March and April. These first-ever planned collisions culminated the experimental stage of a $1 million research effort four years in the making.
Although Consolazio, a UF associate professor of civil engineering and the project's leader, is still crunching the resulting data, his preliminary findings suggest potential new ways to reduce the cost of new bridges - and better safeguard them against the rare but deadly accidental collisions that have cost dozens of lives in the past two decades.
"We now have experimentally measured data that will permit us to improve our analysis and design processes and develop future protection systems," Consolazio says.
The threat of a bridge accident is especially relevant in Florida, where one of the most infamous occurred in 1980 when a freighter brought down a section of the Sunshine Skyway Bridge in St. Petersburg, sending 35 people to their deaths. In 2001, a bridge-vs.-barge incident in Texas killed eight, and 14 motorists died in 2002 when a barge struck the Interstate 40 bridge spanning the Arkansas River in Oklahoma.
While these fatal accidents are rare, non-fatal accidents are far more common. According to a 2003 report by the U.S. Coast Guard and American Waterways Operators, there were 2,692 bridge-vs.-barge accidents involving towing vessels nationwide between 1992 and 2001, with 2,532, or 94 percent, causing less than $100,000 in damage and no injuries or fatalities. Some bridges are struck repeatedly, like the nation's most accident-prone bridge, the EJE Railway Bridge in Illinois, which sustained 170 collisions between 1992 and 2001, the report says.
With its 1,200 miles of coastline and a lengthy Intracoastal Waterway, Florida is a hot spot for barges toting fertilizer, coal, petroleum products and other cargo. Florida has more than 9,000 bridges, including several hundred spanning bays or rivers deep and wide enough for barge traffic, says Henry Bollmann, senior bridge designer at the Florida Department of Transportation.
With no major accidents in recent years, "We've been fortunate in that so far we've had good luck, that the tow boat operators are doing a good job," Bollmann says.
But the threat of accidents results in significantly higher construction costs. State engineers design all bridge supports, or piers, to withstand major hurricane wind forces. But, for bridges in navigable waterways, engineers must design to the far more stringent bridge design collision standards of the American Association of State Highway and Transportation Officials, or AASHTO.
"The major difference is solid, larger, more robust column sections and pile sections - all the substructure components that make up the bridge," Bollmann says. "The other item is that you create connections that are able to carry the bending forces," distributing the collision forces from the point of impact up the pier to the bridge's superstructure and then on to other piers.
The bulked-up construction magnifies expense. Top hurricane wind loads on the Bryant Grady Patton Bridge that replaced the St. George's Island Bridge might have totaled 120,000 lateral pounds, Bollmann says. But the AASHTO standards protecting the bridge against collisions required that some of its piers could sustain 3 million pounds, requirements that at least doubled the bridge cost to $80 million.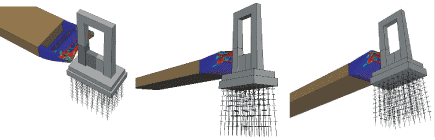
Consolazio says the AASHTO standards are based on "limited test data." Before the St. George Island Bridge experiments, he says, "no one had ever run vessel collision tests on bridge piers at full scale."
Physical preparations for the UF experiments began several months in advance. Consolazio and his team installed dozens of sensors, including load cells, accelerometers, strain gauges and pressure transducers, on the barge and on the two piers the team planned to ram. Research team members David Cowan and Alex Biggs, both civil engineering graduate students, were key contributors to the success of the project, assisting in the design, fabrication and installation of sensor systems, Consolazio says. Additional assistance was provided by civil engineering Professor Ronald Cook, who aided in the design of the impact force measurement system, and former UF civil engineering Assistant Professor Paul Bullock, who installed sensors in the soil surrounding the buried pilings that support the bridge piers.
The sensors aimed to measure not only how much force the collisions generated but also the bridge pier's movement and how the nearby soils responded.
The work intensified once Consolazio, Cowan, Biggs and structures lab technician Charles Broward arrived at St. George's Island for an extended stay that would span more than a month. On the morning of each test, the crew installed several hundred pounds of computer equipment and batteries on the barge and pier, removing it at day's end for safekeeping and to retrieve the data before the next experiment.
High-speed collection of data from the sensors was triggered just prior to impact using optical break-beam sensors mounted to the pier. Once triggered, the data acquisition system gathered and recorded information from the sensor array at a rate of 2,000 samples per second per sensor.
The first collisions targeted a massive pier flanking the shipping channel, which was designed to withstand a major collision. Demolition workers had already removed the road, or superstructure, from the pier and, as with all the experiments, the UF team had no intentions of toppling the pier into the water. But the experiment still involved huge equipment and massive forces.
New Orleans-based Boh Brothers Construction Co., the state's contractor for the new bridge, was a pivotal participant. The company provided the researchers with a tugboat, two barges, related equipment and personnel. The tug pushed the 151-foot-long barge, weighted to 600 tons with two massive concrete spans from the old bridge, toward the pier. Meanwhile, a nearby barge assisted the tug, yanking the collision barge toward the pier with industrial-scale winches pulling thick steel cables.
"The push boat would accelerate the test barge, assisted by the winches, and then just prior to impact, the forces exerted by the tug and winches would be dropped," Consolazio says.
Although the forces involved in the collisions were massive - with some collisions, the engineers measured more than a million pounds of load - the durations were extremely brief.
"The impact loads went from zero to maximum to zero again as the test barge decelerated and rebounded in less than two seconds," Consolazio says.
Consolazio anticipated many of the tests' challenges, including the potential dangers.
"We were very safety conscious because the loads were very large and therefore there was potential for someone getting hurt," he says.
But he had not predicted the dramatic effects of wind, weather, tides and currents.
"On many of the test dates, it was a last-minute call as to whether testing was feasible," he says.
The team rammed the channel pier a total of eight times, sometimes repeatedly in the same day to capitalize on good weather conditions. One reason for the multiple collisions is that the AASHTO code seeks to take into account the impact energy that the barge itself absorbs during impact. Because, for testing purposes, all of the crashes occurred at relatively low speeds and with a barge carrying less weight than often occurs in commercial transport, the UF team needed to ram the barge in the same spot multiple times to gather information relating to higher-energy impacts.
"We accumulated damage with multiple impacts so that we could characterize the deformation that would have occurred if we could have conducted higher-energy impacts," Consolazio says.
The team also conducted seven slower-speed collisions with a smaller pier closer to the shore and farther from the channel. Four of the tests involved a lighter, 280-ton barge and occurred with the road superstructure in place. Those tests sought to determine how much of the impact force was transferred from the point of impact to the bridge deck, or roadway, Consolazio says.
Having collected hundreds of megabytes of data for each test, Consolazio doesn't expect to complete analysis of the data for another 18 months. But his preliminary findings, prepared for a paper he plans to present at an upcoming Transportation Research Board conference, suggest that for massive piers similar in nature to the channel pier that was tested, the maximum impact loads generated may be less than what AASHTO predicts.
"From our higher-energy impact test data, the maximum impact load we measured was 1.05 million pounds," Consolazio says. "If you compare that load to the corresponding value predicted by the AASHTO specifications, the specifications would predict much higher loads. However, we are examining this in further detail because several AASHTO load-modification factors are lumped together that might ultimately affect this comparison."
Part of the disparity appears to be tied to the barge sustaining so much of the collision's force.
"Barge deformation limits the amount of load that can be generated. Think of a soft, deformable object colliding with a rigid concrete pier - the load that's generated is controlled by the softer of the two systems," he says, adding that some accidental collisions have resulted in gashes to barge hulls as large as 15 feet in depth.
The reduced load, if confirmed, could ease some of the expensive construction requirements in the AASHTO code for collision-prone piers. Even more important, the new data together with Consolazio's newly proposed collision analysis techniques will help better ensure bridge safety. Whereas the current design specifications are based on the use of static, or permanent, load forces, Consolazio's results stem from the real world of dynamic, or time-varying, events.
UF civil engineering faculty have already revolutionized bridge design by developing FB-Pier, software that uses three-dimensional modeling and non-linear solid mechanics to improve the design process. Consolazio's results could further refine the program.
"Knowing that these are dynamic events and knowing what the durations of the loads are, we can now develop design methods or protection systems that exploit dynamic instead of static behavior," Consolazio says.
Gary Consolazio
Associate Professor, Department of Civil and Coastal Engineering
(352) 392-9537 ext. 1510 grc@ufl.edu
Related Web site:
http://www.ce.ufl.edu/~grc/
|